【高新产业链观察】我国碳纤维产业的发展及龙头企业梳理
碳纤维因具有无可比拟的优异性能,是航空航天、国防和民用高科技领域不可或缺的关键战略材料,是我国战略性新兴产业新材料领域中最主要的发展方向之一。碳纤维产业长期由日本和欧美巨头主导,以中国为代表的新兴经济体呈追赶之势。目前我国形成了以江苏、山东和吉林等地为主的碳纤维产业聚集地,主要厂商有中复神鹰、碳谷+宝旌、江苏恒神、光威复材、中简科技等。在政策大力扶持、国产化替代加速、下游需求快速增长等利好因素带动下,我国碳纤维行业快速发展,但由于技术和工艺水平相对落后,供给端处于紧张局面。这在航空航天领域高性能碳纤维上体现得尤为明显。目前在航空航天高性能碳纤维批量供应方面领先的国内企业主要是中简科技。
一、碳纤维产业链基本结构
(一)碳纤维的定义
碳纤维(Carbon Fiber,简称 CF)是由有机纤维(粘胶基、沥青基、聚丙烯腈基纤维等)在1000的高温环境下裂解碳化形成的含碳量高于90%的无机纤维,不仅具有碳材料的固有本征特性,又兼备纺织纤维的柔软可加工性。作为一种国家亟需、应用前景广阔的战略性新材料,碳纤维具有目前其他材料无可比拟的高比强度(强度比密度)及高比刚度(模量比密度)性能,还具有耐腐蚀、耐疲劳等特性。相较其他材料,碳纤维复合材料密度最低,因此在轻量化、高强、高模等应用领域,碳纤维复合材料的性能优势明显。
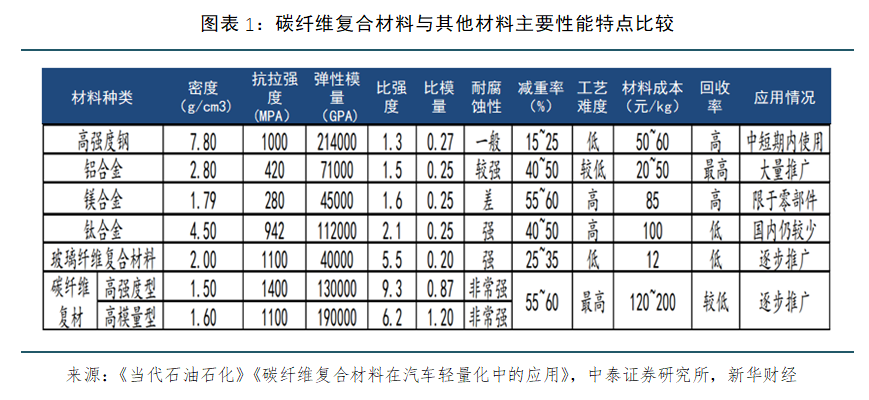
碳纤维可以按照原丝类型、形态、力学性能等不同维度进行分类。按照原丝种类,由聚丙烯腈(PAN)原丝生产出的聚丙烯腈(PAN)基碳纤维占据主流地位,产量占碳纤维总量的 90%以上。碳纤维按力学性能分为通用型和高性能型。通用型碳纤维强度为1000MPa、模量为 100GPa 左右。高性能型碳纤维又分为高强型(强度 2000MPa、模量 250GPa) 和高模型(模量 300GPa 以上)。强度大于 4000MPa 的又称为超高强型;模量大于 450GPa 的称为超高模型。在实际使用中,龙头企业日本东丽的产品编号通常被作为行业标准,如日本东丽的碳纤维产品编号有T300、T800、M30等多种,其中T表示强度,M表示模量。强度上,T后缀的数字越大代表产品的强度越大;模量上,M后缀的数字越大代表产品的模量越大。
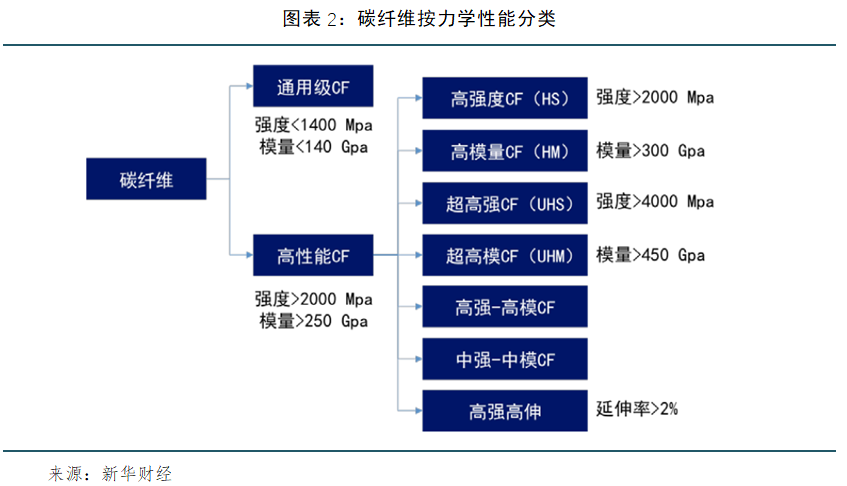
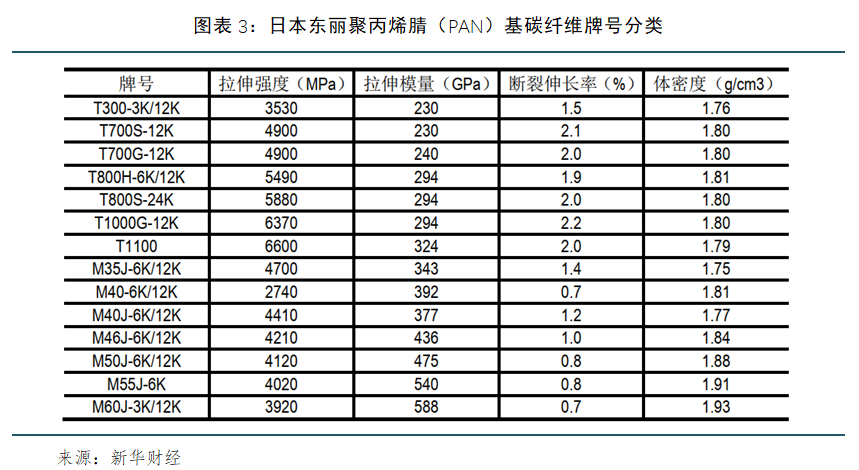
碳纤维按用途可分为宇航级和工业级两类,也被称为小丝束和大丝束。宇航级(小丝束)碳纤维初期以1K、3K、6K为主,逐渐发展为12K和24K,主要应用于国防工业和高技术,以及体育休闲用品(如飞机、导弹、火箭、卫星和钓鱼杆、高尔夫球杆、网球拍等)。工业级(大丝束)碳纤维通常指48K及以上碳纤维,包括60K、120K、360K和480K等,应用于不同民用工业,包括纺织、医药卫生、机电、土木建筑、交通运输和能源等。在按丝束大小分类中,K表示碳纤维单丝的数量,如1K代表一束纤维丝里包含了1000根单丝。小丝束碳纤维在工艺控制上要求更严格,碳化等设备造价高,大丝束碳纤维成本相对较低,具有更高的性价比。
(二)碳纤维产业链结构
碳纤维生产流程长,工序多而复杂,工艺、技术和资金壁垒很高。完整的碳纤维产业链包含从一次能源到终端应用的完整制造过程。产业链上游企业从石油、煤炭、天然气均可以得到丙烯,丙烯经氨氧化后得到丙烯腈,丙烯腈聚合和纺丝之后得到聚丙烯腈(PAN) 原丝;产业链中下游企业再经过预氧化、低温和高温碳化后得到碳纤维,并可制成碳纤维织物和碳纤维预浸料,作为生产碳纤维复合材料的原材料;碳纤维经与树脂、陶瓷等材料结合,形成碳纤维复合材料,最后由各种成型工艺得到下游应用需要的最终产品。
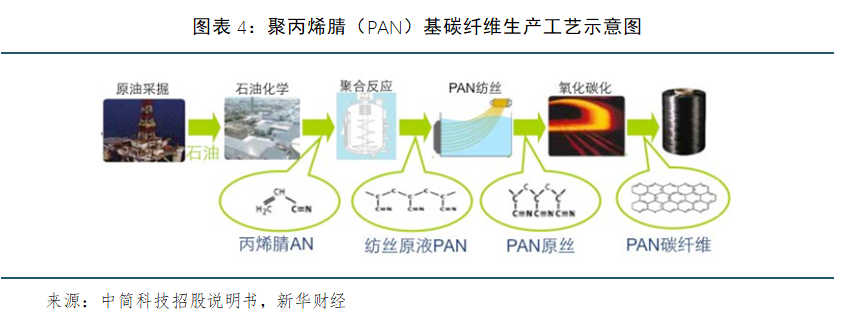
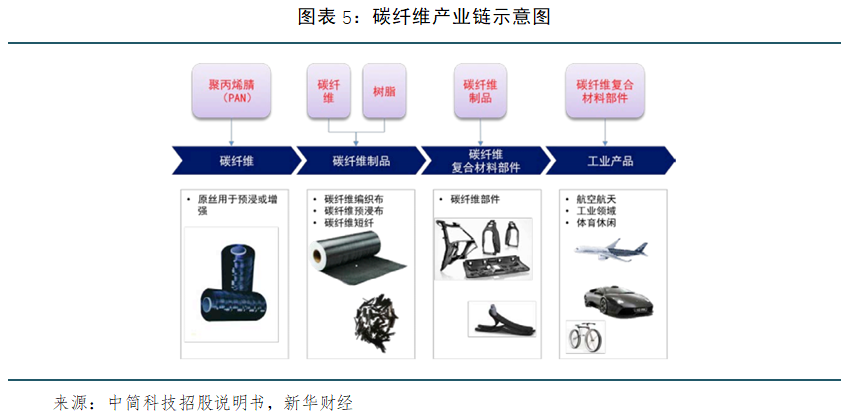
碳纤维原丝制备是碳纤维产业链的核心环节,碳纤维原丝的质量和成本很大程度上决定了碳纤维的质量和生产成本。碳纤维原丝制备占碳纤维生产成本的一半以上,其性价比与供应稳定性是碳纤维产业链的重要影响因素,直接影响着碳纤维的应用领域的广度。对于碳纤维原丝,经过长期技术研发与工程化实践,国际上形成了湿法纺丝和干喷湿法纺丝两种原丝制备工艺。相较湿法纺丝,干喷湿法纺丝可以进行高倍的喷丝头拉伸,纺丝速度是湿法的 3-4 倍,明显提升了生产效率同时降低了生产成本。不过由于干喷湿纺工艺技术难度大,目前世界上仅少量企业掌握该生产技术并形成成熟的碳纤维产品。
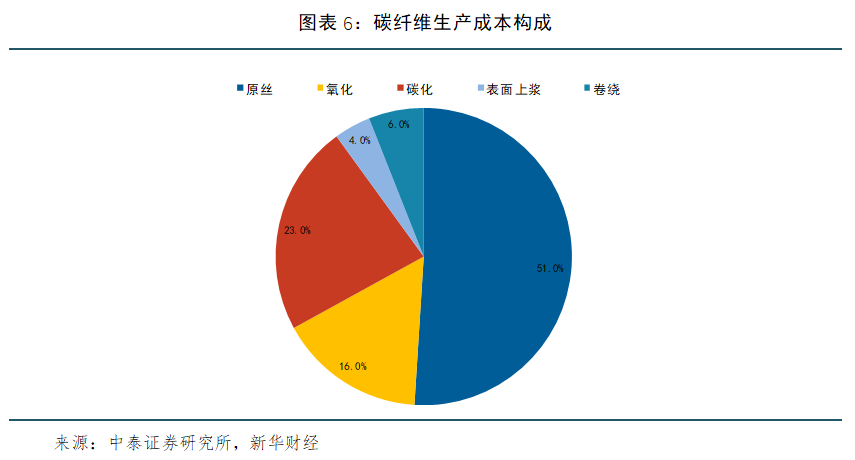
二、碳纤维产业链主要玩家及竞争格局
从全球产能区域分布来看,美国、中国和日本产能最大。根据《2020全球碳纤维复合材料市场报告》统计,2020年全球碳纤维运行产能约17.2万吨。分区域来看,美国运行产能3.7万吨,占全球22%;中国大陆位居第二,运行产能3.6万吨,占比21%;日本位列第三,运行产能2.9万吨,占比17%。日本和欧美传统巨头基本完成国际产业基地的布局,主导着全球碳纤维行业。同时新兴经济体在迅速追赶中,尤其是中国。
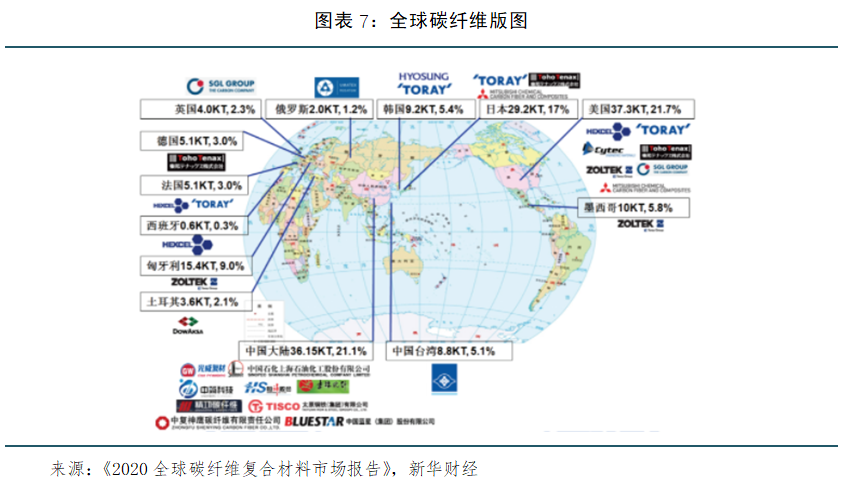
全球碳纤维特别是高性能碳纤维由日本、欧美企业所垄断。目前,全球前五大企业为日本东丽(美国卓尔泰克被东丽收购)、德国西格里、日本三菱丽阳、日本东邦、美国赫氏,2020年合计市占率62%。日本是全球最主要的碳纤维生产国,世界碳纤维技术主要掌握在日本公司手中,其生产的碳纤维无论质量还是数量上均处于世界领先地位,日本东丽更是世界上高性能碳纤维研究与生产领域的“领头羊”。东丽与卓尔泰克合并后,总产能在位列第一,约5.37万吨。西格丽集团和三菱丽阳分别位列第二和第三,产能分别为1.48万吨和1.41万吨。
在全球小丝束碳纤维市场竞争中,日本企业垄断地位更加明显。根据中国化学纤维工业协会的数据,2020年,日本东丽、东邦和三菱三家占据全球小丝束碳纤维市场份额的49%。其中日本东丽产能占全球小丝束总产能的26%,东邦小丝束产能占全球小丝束总产能的13%,三菱占10%排第三。在全球大丝束碳纤维市场竞争中,美国赫氏为全球主要的大丝束供应商,2020年占据了58%的全球市场份额,其次是占比31%的德国SGL和占比9%的日本三菱。
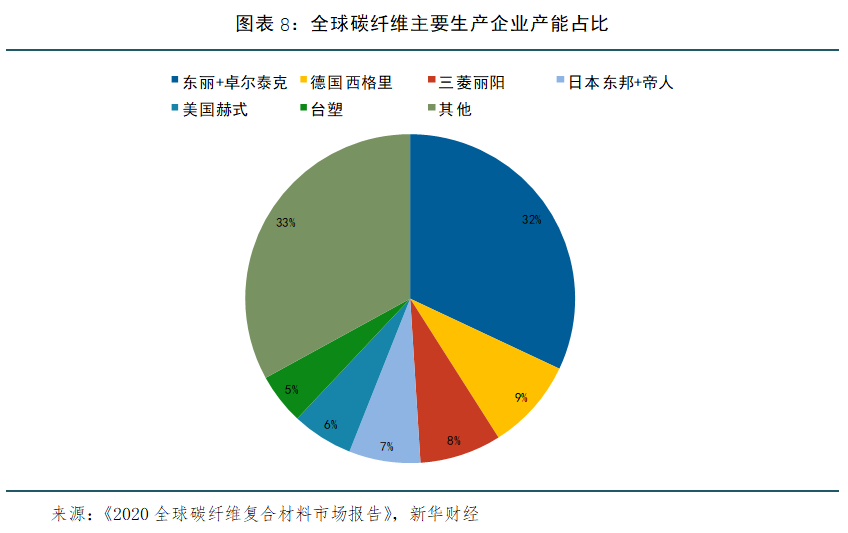
受限于技术封锁等多重因素,国内碳纤维行业发展曲折。国外碳纤维企业通过技术及价格优势打压国内碳纤维企业,使我国的碳纤维市场长期受制于欧美及日本等国家。长期以来,国内碳纤维市场中进口碳纤维的供给量远超国产碳纤维。2020年国产碳纤维供给量为1.84万吨,占国内需求的比重仅为38%。由于较多国产碳纤维企业尚未实现关键技术的突破,生产线运行及产品质量不稳定,国产碳纤维行业长期存在“有产能,无产量”的现象。目前碳纤维市场仍处于供不应求的状态。2020年受疫情影响,国外碳纤维出口国内的难度加大,加之最近两年日本、美国加强了对碳纤维出口中国的政策管控,导致国内碳纤维境外供应难度进一步加大。
碳纤维特别是高性能碳纤维作为国防战略新材料,其价格不仅仅只遵循市场规律,还与供需两端国家的国防政策有关。随着国产高性能碳纤维技术和产业化的不断发展,为确保国防安全,避免长期受制于人和国外企业垄断国内市场,国家出台相关政策,大力扶持国产高性能碳纤维在航空航天等国防领域的广泛应用。我国在碳纤维行业技术、产品、成本等方面快速突破与追赶,初步形成了以江苏、山东和吉林等地为主的碳纤维产业聚集地。
目前,国内碳纤维产能居前厂商主要有中复神鹰、碳谷+宝旌、江苏恒神、光威复材、中简科技等。2020年,中复神鹰、碳谷+宝旌的产能超过8000吨,江苏恒神的产能超过5000吨,光威复材的产能超过5000吨。而且这些头部企业都在快速扩张产能。根据中复神鹰官网介绍,2021年9月,中复神鹰万吨级碳纤维产线投产,碳纤维产能规模达13500吨。根据光威复材公告,包头拟新建万吨产线,预计2022年新增产能4000吨,合计达7855吨,后续6000吨产能逐步投产。根据《2020全球碳纤维复合材料市场报告》预测,“3-5年内,全球产能排名会有剧烈的变化,能进入世界前十名的起码需要万吨以上产能,中国厂家预计有5家企业入围前十名。全中国的碳纤维产能有望超过世界产能的50%,成为最大生产国”。
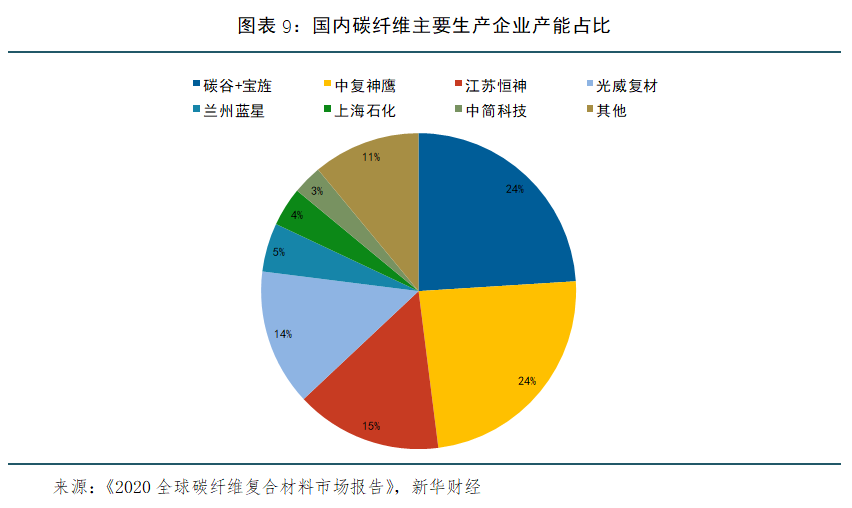
三、碳纤维在航空航天领域的发展和龙头企业
(一)航空航天碳纤维发展趋势
碳纤维的应用领域十分广泛,从发展历史来看,航空航天领域是主要的驱动力。应用在航空航天领域的碳纤维属于高性能产品,是碳纤维生产技术和工艺的制高点。2020年全球航空航天碳纤维需求量为1.6万吨,占比约15%,但由于航空航天领域用碳纤维单价高,因此航空航天碳纤维市场规模较高,2020年达9.9亿美元,占碳纤维整体市场规模的38%。从需求结构来看,我国航空航天领域碳纤维需求占比仅3.5%,远低于美国和日本,有着极大的市场提升空间。
未来我国航空航天领域对高性能碳纤维需求保持较高增速。一方面,高性能碳纤维是高精尖航空航天应用的重要原材料,西方先进企业长期处于垄断地位,且对我国实行严格的禁运措施。随着国内高性能碳纤维制备技术逐渐成熟、同级别产品性能指标可以达到甚至赶超国外先进水平,高性能碳纤维的国产替代进程不断加速。2016年我国国产碳纤维占市场总体需求量的比例为18.4%,2020年这一占比上升至37.9%。根据赛奥碳纤维的预测,国产碳纤维需求量有望在2025年之前超过进口碳纤维。另一方面,碳纤维结构件相比传统金属结构件重量降低约20%-40%,并克服了金属材料容易出现疲劳和被腐蚀的缺点,碳纤维结构件的良好成型性也可以使结构设计成本和制造成本大幅度降低。基于碳纤维材料在性能方面和经济方面的较大优势,高性能碳纤维在航空航天领域应用占比不断提升,大大提高了该领域的总体需求量。
在航空领域,碳纤维复合材料自20世纪70年代以来首次被应用在飞机上的一些二级结构,如整流罩、控制仪表盘和机舱门等。近三十年来,随着高性能碳纤维和预浸料-热压罐整体成型工艺的成熟,碳纤维复合材料的使用逐步进入到机翼、机身等受力大、尺寸大的主承力结构中。近年来,碳纤维复合材料在军用飞机上的用量逐年增加。由于碳纤维复合材料具有低密度、高比强度、高比模量、可设计性强等优点,在飞机上采用碳纤维复合材料可以大幅度减轻机体结构质量、改善气动弹性,提高飞机的综合性能,大批量飞机零部件相继采用碳纤维复合材料,并且采用复合材料的面积、部位和重量也日趋增加。

在航天领域,碳纤维复合材料作为结构功能一体化构件,最早被用于人造卫星天线和卫星支架的制造;又因其耐热耐疲劳的特性,碳纤维也广泛应用于固体火箭发动机壳体和喷管上。我国的神舟一号到神舟九号飞船,其飞船推进分离系统的主承力部件就是由碳纤维复合材料制造。
我国高性能碳纤维供应长期面临紧张局面。如前所述,高性能碳纤维分为高强度碳纤维与高模量石墨纤维。高强度碳纤维方面,目前公开市场上性能最高的为日本东丽的T1100级碳纤维,且其制备技术对我国实行严格的技术封锁。我国领先碳纤维企业具备了批量稳定生产T800级碳纤维的技术,并且在实验室制备的T1000/T1100级碳纤维主体性能达标,并具备了工业化生产的能力。高模量碳纤维方面,目前公开市场上性能最高的为日本东丽的M65J级石墨纤维,我国领先碳纤维企业可批量稳定生产M55J级碳纤维并应用于航空航天领域,目前尚未掌握M60J及以上高模量石墨纤维批量稳定制备技术。
长期以来,我国碳纤维市场围绕体育休闲产业等中低端领域发展,能够生产符合航空航天标准的高性能碳纤维企业屈指可数。目前国内在航空航天领域实现大规模产品应用的碳纤维供应商只有中简科技和光威复材,且产能利用率均处于较高水平,因此,高性能碳纤维市场供给较为紧张。在未来需求快速增长的背景下,国内高性能碳纤维市场供给将长期处于紧张局面。
(二)航空航天碳纤维的龙头企业
国内产能居前的中复神鹰、吉林碳谷、光威复材等都有应用于航空航天领域的高性能碳纤维产品,而专注于高性能碳纤维产品的国内代表企业为中简科技。其通过多年技术积累,突破了高于T700级碳纤维的工程产业化技术,打破了国外对航空航天领域高端碳纤维的封锁。中简科技规模化生产的产品和主要收入来源为ZT7系列。由于专注于高端产品,中简科技碳纤维产品附加值及利润水平处在领先地位。
根据公司招股说明书,中简科技是我国高性能碳纤维技术研发和工程产业化稳定生产的领跑者,在我国率先实现ZT7系列碳纤维稳定批量生产并应用于航空航天高端领域,在高于T700级碳纤维批量供应方面处于领先地位。其生产的ZT7系列碳纤维所用的技术均为自主研发,具有完全自主知识产权;生产工艺实现自主开发,生产设备98%为自主设计,关键设备全部实现国产化;生产所用关键原辅料均为国内配套或自制;核心控制系统采用国产化DCS自动系统。性能方面,其ZT7系列碳纤维对日本东丽T700级碳纤维形成超越。ZT7系列碳纤维力学性能介于日本东丽T700级与美国IM7之间,拉伸模量高于东丽T700级碳纤维,综合性能优于日本东丽T700S级碳纤维。
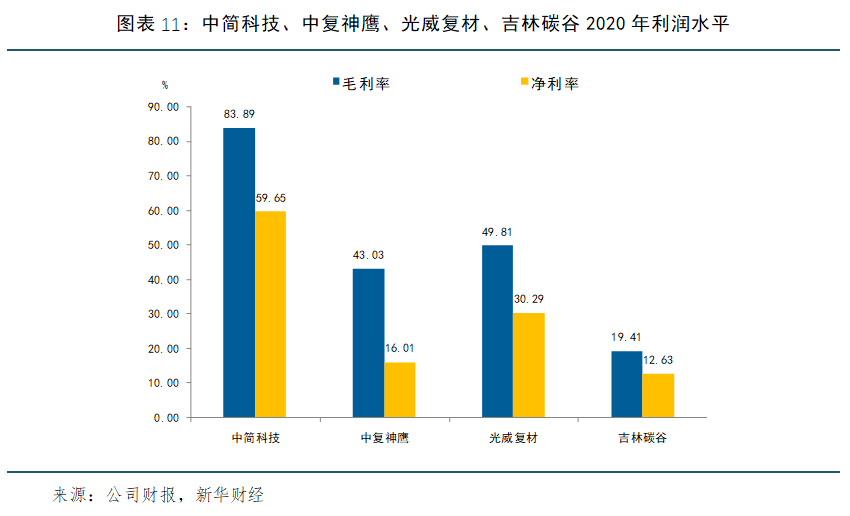
中简科技未来产能扩张计划庞大。中简科技原仅拥有一条150吨/年(12K)或50吨/年(3K)的生产线,产能瓶颈较大。2019年,首次公开发行股票募集资金2.21亿元用于1000吨/年(12K)国产T700级碳纤维扩建项目,该项目于2020年3月完成设备调试,2021年9月千吨线等同性验证通过评审,2021年12月底公司表示千吨线已正式投产。随着产能逐步释放,中简科技在高性能碳纤维领域的发展空间更大。公告显示,2019年公司ZT7系列(高于T700级)碳纤维实际产量90.61吨,实际销量79.86吨;2020年产量达到114.08吨,同比增长25.90%,销量116.16吨,同比增长45.47%。2021年10月,中简科技发布向特定对象发行股票募集说明书,拟募资20亿元,16.5亿元投入高性能碳纤维及织物产品项目(项目总投资18.67亿元),建设周期四年,建成后将新增产能1500吨/年(12K),合计产能2500吨/年(12K)。项目投产后正常年份,测算带来年销售额为17.16亿元,而2020年中简科技实现年收入3.9亿元,净利润2.32亿元。
对比来看其他家碳纤维龙头企业,虽然总体规模大,但规模化的型号主要为T300级,用于民品居多。光威复材规模化生产的碳纤维型号为GQ3522(T300级),是其主要的收入和利润来源。恒神股份目前规模化生产的碳纤维型号为HF10(T300级碳纤维)。中复神鹰2020年航空航天领域碳纤维产品销量为254.91吨,占其碳纤维产品总销量(3761.14吨)的6.78%。中复神鹰以民品碳纤维销售为主,销售单价大幅低于以军品业务为主的光威复材、中简科技,因此其碳纤维业务销售收入低于光威复材。中复神鹰、光威复材及恒神股份的碳纤维产品种类基本相当,基本实现了对T300级至T1000级、M40级别的产品覆盖,中简科技未生产T300级产品,专注于高性能产品。
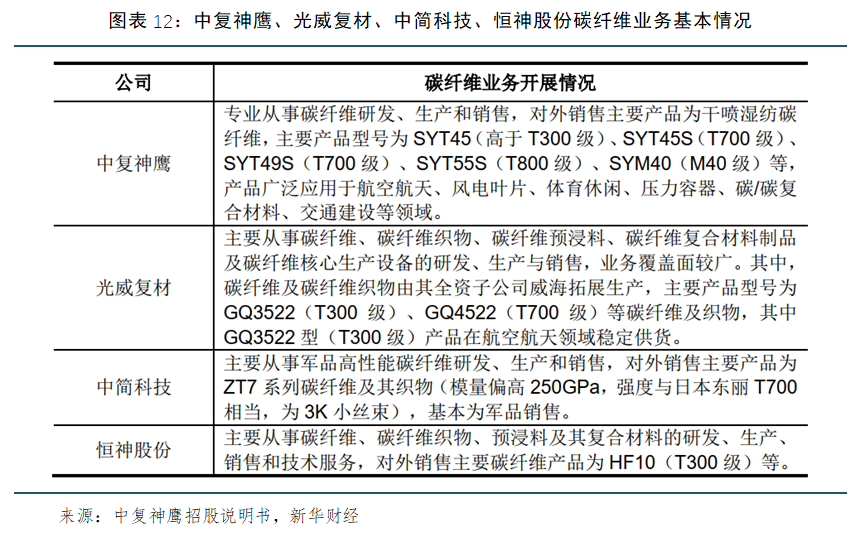
(文章来源:新华财经)
本文来源于网友自行发布,不代表本站立场,转载联系作者并注明出处